Topic 8 - Highly Commended
The Northstone Materials Tile Plant in Toome has been manufacturing and supplying a range of high quality roof tiles and accessories to customers in Northern Ireland, the Republic of Ireland and Great Britain for 14 years. After years of development and improvement, the factory now has the potential to produce up to 65 - 70,000 tiles per day, approx 1.8 million tiles per month. They use automated machinery to compress a semi-dry concrete mix onto a tile mould which is then cured in ovens. After curing, the mould is removed to leave a dry concrete tile which is painted for consistency in colour and packed onto pallets to be sold.
The Tile Plant has achieved ISO 45001, ISO 14001 and ISO 9001. It is regularly inspected by the Health and Safety Executive Northern Ireland.
In 2020 and 2021 respectively a new Manager and Assistant Manager – Hugh Bradley and Aaron Quinn – were appointed. Since this change in management, the tile plant has focused on creating an open and honest atmosphere to encourage the workforce to suggest healthy, safe, environmental and operational improvements. By empowering their team to be positive and think proactively, the tile plant has and continue to implement many valuable improvements.
As part of the ongoing initiative to increase employee engagement, a range of health and safety issues and potential solutions were raised by employees for discussion with the local management team at safety meetings and employee consultations. Key low-cost improvements implemented include:
- Talent Learning Management System (LMS) –Training management software designed to familiarise new employees with the process line and terminology through interactive overview videos before entering the plant. Introduced by the manager after recognising that new starters had varying levels of process line knowledge despite training. Reduces likelihood of injury from inexperience (human factors). Still in trial stages and will be continually improved.
- Beacon Installation – A beacon was installed outside the factory that alerts forklift drivers when skips inside are full. Issue and solution identified by factory operative, Adrian Purdy, who would previously have left his station inside to alert forklift drivers outside. This has reduced unnecessary pedestrian movement in the busy yard.
- Grid Installation – Grid fabricated inhouse and installed over waste concrete skip to prevent tile moulds from falling in. Originally raised on the ‘Fix What Bugs You’ whiteboard and implemented by operative Rainers Rirdancis. Risk of back strain removed as operatives are no longer required to reach into the skip to collect fallen moulds.
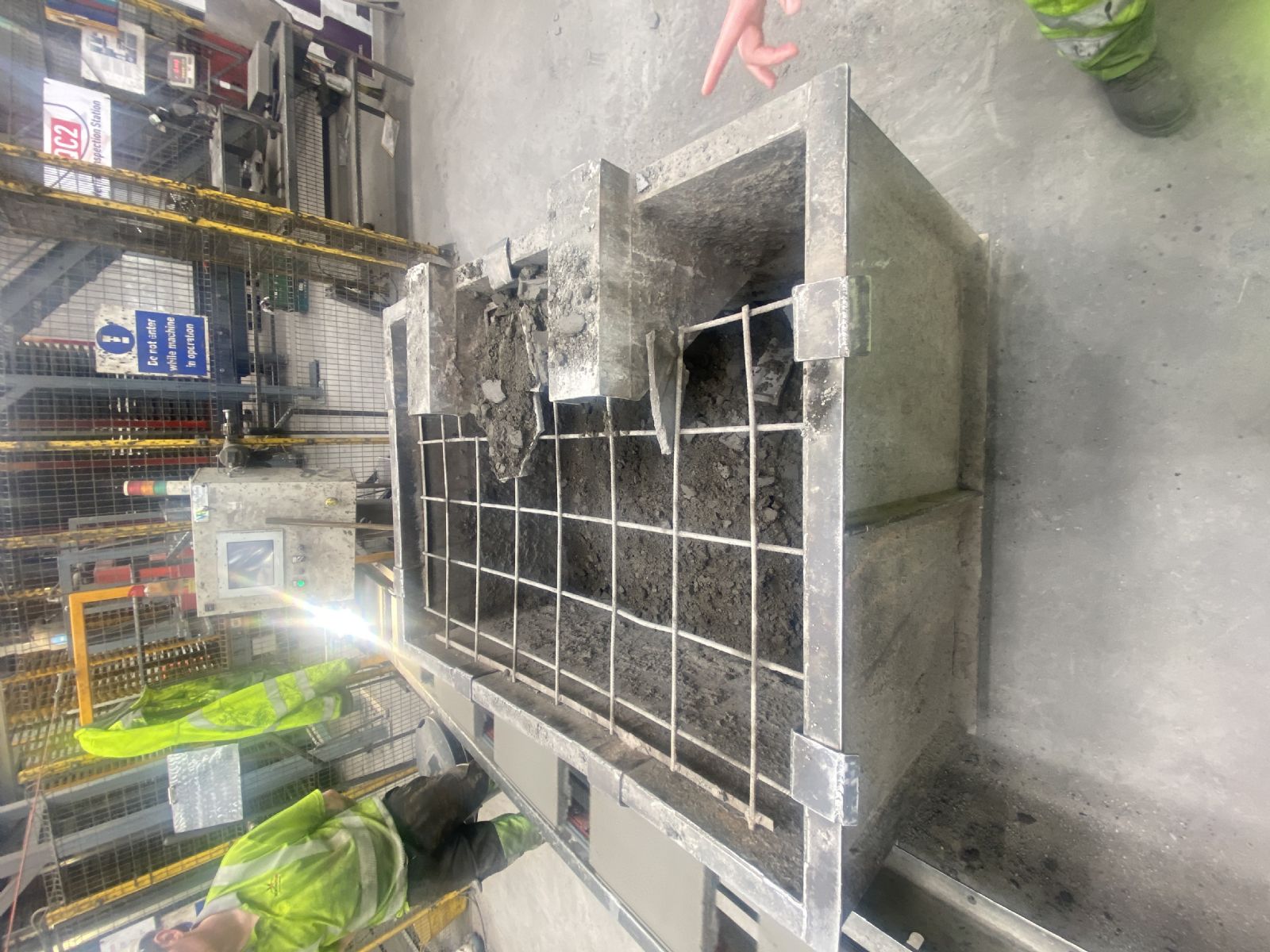
- Disposable Hi-Vis – Complaints raised by paint operatives regarding paint not washing out of hi-vis PPE. This compromises PPE reflectiveness. Jessica Halton, purchasing clerk, sourced disposal hi-vis PPE suits and employees are encouraged to change these frequently to remain visible.
- Retractable Hose – Several operatives raised concern about loose hoses not being tidied away. Retractable airline hoses were installed across the plant to reduce this potential trip hazard.
- Housekeeping – Stores re-organised so heavy parts stored on bottom shelves. Re-organisation encouraged by consultancy firm Outform who were employed by the plant to improve efficiency and safety. Reduces likelihood of parts rolling from shelf and injuring operatives.
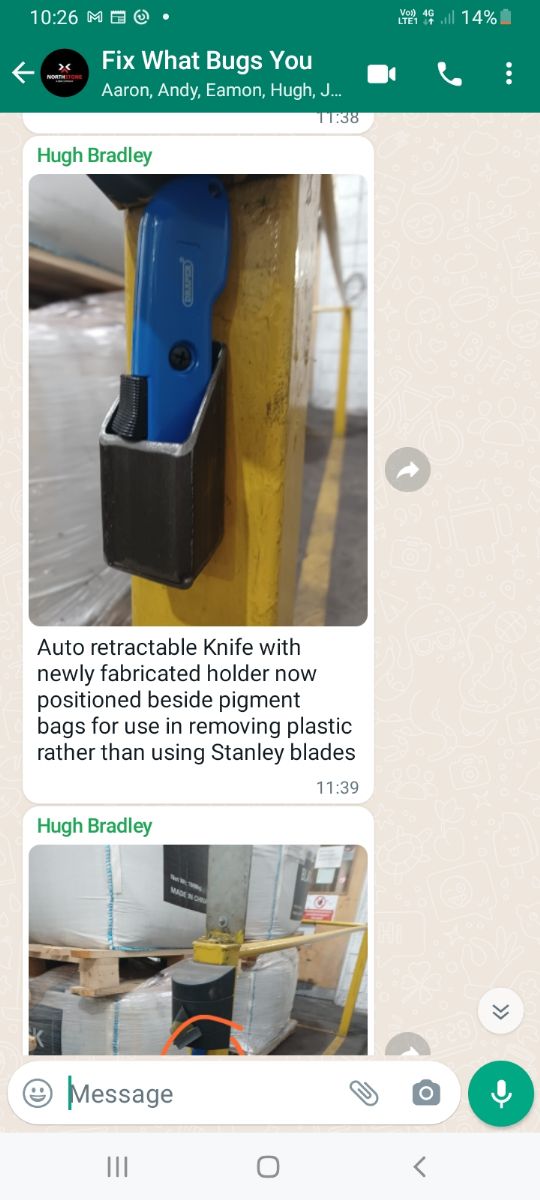
- 7. Auto Retractable Knife – Hugh Bradley (manager) commissioned the fabrication of an auto retractable knife holder to reduce risk of injury when opening pigment bags. Operatives had previously raised issue with having to use loose stanley blades to open the bags on the ‘Fix What Bugs You’ WhatsApp group. The holder also encourages better housekeeping.
These improvements have required minimal investment but brought significant benefits. They have proved successful with positive feedback received from operatives and management at weekly team meetings.
The team have actively focused on collaboration and teamwork which has driven a positive safety culture where employees are engaged and feel valued. Although each individual improvement may appear relatively minor considering the minimal investment required, when accumulated they have made a significant difference at the plant and most importantly have created a more enjoyable, safer workplace where employees feel valued.
Please see additional pdf for more information